download:Development plan of plasma-resistant FFKM used in dry process of opto-electronics .pdf
KTSEAL CO., LTD.
Development plan of plasma-resistant FFKM used in dry process of opto-electronics
“Deep plough own brands, stand firmly in Taiwan market”, “move forward to China, key eyes on the whole world” Adhering to the concept of continuously improving the product and service quality and firmly believing that “good quality comes from strict requirements”, KTSEAL motivates the staff to learn and develop by themselves through good regime, which will make the company develop and improve customers’ competitiveness with KTSEAL products. Through exchange and cooperation with the academic community, the product quality and added value will also be improved.
- Establishment date/ March 20, 2003
- Principal/ Li Peiming
- Capital sum/ 25,000,000 TWD
- Staff number/ 30
Plan reason
As most domestic petroleum manufacturers have no independently developed fluororubber, and DUPONT and GREEN TWEED have occupied most of the market, the commercially available foreign fluoroether rubber (DAIKIN, 3M, SOLVEY, AGC and other large manufacturers are determined currently) will be used in this plan, which will be mixed with various functional additives developed independently in domestic for mixed refining, so as to change its nature and achieve special functions; in addition, with the special cross-linking and clean method of the company, the fluororubber seal assembly meeting the demand of dry process in opto-electronics industry will be developed, whose cleanliness degree is also acceptable in opto-electronics industry; with the help of research resource from research units at home and abroad, establish the cross-linking system of fluoroether rubber, so as to lay the foundation of developing new materials in the future, jointly develop the fluoroether rubber seal assembly meeting the demand in opto-electronics industry, and compete with those large manufacturers such as DUPONT and GREEN TWEED.
Introduction of new product
Introduction of new product
In this plan, we mainly use the fluoroether rubber of high fluorine content, utilize the existing open and special mixed refining procedure of the company, add various functional additives developed independently in domestic to change its nature and achieve special functions; in addition, with the special cross-linking and clean method of the company, the fluororubber seal assembly meeting the demand of dry manufacture procedure in opto-electronics industry will be developed, whose cleanliness degree is also acceptable in opto-electronics industry.
This product mainly features excellent weight loss rate and low dust dissipation in plasma environment, which can be used as the best solution in dry etching processes.
Key points of plan innovation
Key points of plan innovation
The core technology of this plan is utilizing the open mixed refining method plus special and vacuum cross-linking process, so as to prepare the viton seal assembly that can resist corrosive gas. With the help of open mixed refining process, we can know about the change of rubber material and dispersion of additives during mixed refining. What’s more, the vacuum cross-linking can significantly improve the cross-linking density of rubber materials and improve the product quality.
For most of fluororubbers, two cross-linking steps are required, with first step aiming at initial forming of product and obtaining necessary shape and second step aiming at increasing the cross-linking density of product, so as to ensure the cross-linking integrity.
In this plan, the second cross-linking will occur in vacuum environment, so as to ensure the small molecular substances in the fluororubber and unreacted cross-linking agents can dissipate better in vacuum environment, in which way the terminal customers do not have to worry about volatilization of small molecule substances or dust dissipation and product pollution.
Research achievements and derivative benefits
The completion of this plan can reduce the customers’ dependence on imported products. Based on the business volume of our company, the sales volume will increase by 700 pieces during initial stage, which means the output value will increase by approx. 700 (PIECE) ×10,000 (TWD/PIECE) =7 million TWD at the end of 2015 (10,000 TWD/piece).
Afterwards, 25% stable growth can be maintained, with the sales volume increasing by 875 pieces within one year after closeout (end of 2016), and sales amount increasing by 875 (PIECE) × 10,000 (TWD/PIECE) =8.75 million TWD. In long term (end of 2017), the sales volume can increase by approx. 1,095 pieces, and the sales amount will increase by 1,095 (PIECE) × 10,000 (TWD/PIECE) =10.95 million TWD. It is predicted that the sales amount will increase by approx. 7 million TWD + 8.75 million TWD + 10.95 million TWD = 26.7 million TWD within 3 years after closeout.
In addition, during investment promotion, to ensure the output of this plan, the company is now expanding the clean room and purchasing related equipments, with predicted investment amount increasing by 1 million TWD.
After completion of this plan, a product contending with KALREZ®4079 will be developed in the year of closeout; in the future, to meet the demand of end customers, the products and after-sales service of each product corresponding to different plasma etching will be derived, and it is predicted that 10 products or services will be derived within 3 years after closeout.
Important experience of project execution
The development journey is tough, and the strength of a team is larger than an individual, with the professional guidance (material, processing, inspection, etc.) about rubber provided by technology transferring units in the plan, the company can break through the current technology and step into different fields.
The company’s primary business is rubber molding, and the experience in mixed refining of rubber materials is more or less insufficient. The completion of this plan will promote the company to establish new business department, and introduce the mixed refining of rubber materials and formula adjustment into the molding factory as well as the professional fields of material technology guidance, which will improve the company’s profits. The development of rubber material process is a new challenge to the company staff, and the training is also very hard, however, the enriching of knowledge and accumulation of practical experience will become the energy of the company staff and also the company’s property.
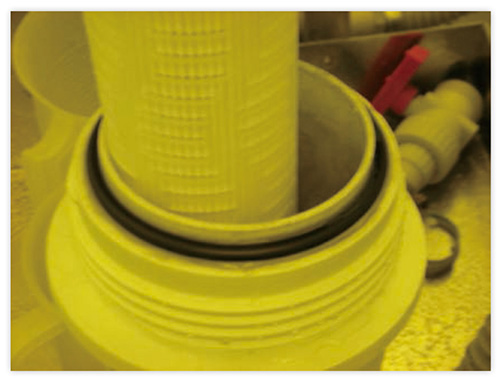
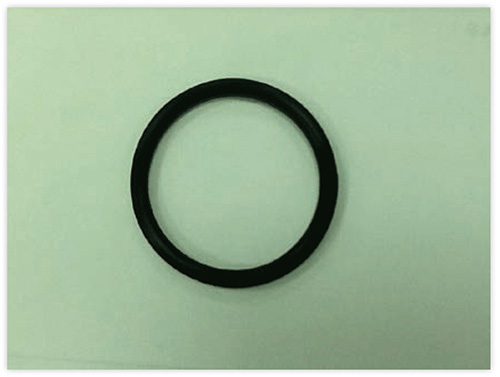
Chemistry for People’s Livelihood
Compilation of research results about assisting traditional industry in technology development in 2015